Automation and digitization are revolutionizing nearly every industry in the world, even old-school construction. Contractors and developers are leaning into this technology as it becomes more commonplace, and they see an increased need for enhanced productivity, quality, and safety due to continued urbanization.
As a result, the construction robot market will reach $166.4M by 2023, up from $76.6M in 2018. From design through final inspection, robotics transforms the way we build the country’s infrastructure, jettisoning construction into the new age. Utilizing these tools significantly alters many crucial tasks, including design translation, 3D printing structures, task repetition, progress tracking, and job site safety.
To know more about the impact and the applications of automation and robotics in construction, we at RoboticsBiz connected with Raffi Holzer – co-founder, and CEO of Avvir, a software platform company based in NYC, reshaping the way project owners and contractors manage construction progress. Avvir employs computer vision and deep learning to provide automated construction verification and progress monitoring.
He was happy to answer our questions and walk us through more details, including use cases and where he sees the industry heading next.
You can read the complete interview below.
1. Architects, engineers, and all other construction process participants integrate advanced construction methods today due to the high complexity of the construction process. What roles do automation play to revolutionize various stages of the construction life-cycle? What are the key benefits?
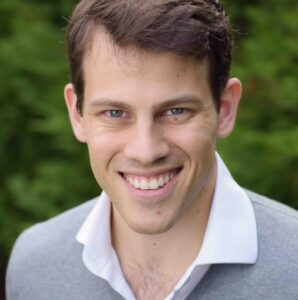
Automation at its heart is about extending the productivity of human beings. Within construction, there are a plethora of dangerous, dirty, or simply repetitive tasks that machines or computers would be better suited to handling than human beings. Everything from tying rebar, to shoveling dirt, to hanging drywall could be improved at some level from automation, and there are startups active in each of those spaces today. The opportunity is massive. Construction productivity has stalled, and if we as a society are going to solve problems around things like affordable housing while overcoming a skilled labor shortage, robotics and automation will necessarily have a large part to play.
2. Robots in the construction sites take over the tasks of handling heavy loads, performing dirty or dangerous work, or working at hardly accessible locations and in unfavorable physical positions. Right now, they function as tools of the human being, but can they be developed as intelligent and autonomous tools? Or, are fully automatic systems suitable in construction?
Fully autonomous systems operating on a construction site are certainly a theoretical possibility. But we’re at least as far away from that reality as we are from truly autonomous vehicles. For now, I think the right focus is on automated systems that function as labor augmentation or enhancement. For one, those sorts of systems are simply more achievable in the short term. Second, they are simply less scary to most people worried about the loss of control, and even their job, so they are likely to be more quickly adopted. I think the analogy to vehicles is actually pretty instructive. You start with lane assist and intelligent cruise control. Eventually, you graduate to full autonomy.
3. What are the factors restraining the automation and robotics systems implementation in the construction sites? What are the key short and long-term challenges in the adaptation of robotics technology?
I think the key factors holding automation back in construction are twofold. First, people are scared of automation taking their jobs. The second is accounting. General contractors operate each project independently. Each needs to see an immediate return on investment on any innovation. Unfortunately, innovation doesn’t work that way. The kinks typically need to be worked out, and it often takes a couple of projects to prove our returns. Because each project represents its P&L, there is typically no single stakeholder for whom it makes sense to make that initial investment. This results in institutionalized short-term thinking.
4. Tell us about Avvir and how it solves the existing challenges.
Our technology is focused not on the automation of labor in the classic sense but on the automation of data gathering, analysis, and reporting. We compare reality capture data to building plans and schedules using a set of machine learning algorithms to automatically generate progress reports, earned value reports, and perform QA/QC checks. Avvir’s approach to overcoming the obstacles to adoption starts with acknowledging them. We recognize that we are not going to change the industry alone. We work to identify change agents within the industry and then act as enablers because that is what automation technology can do well: enable and empower people.
5. What are the technological advancements expected to happen in the next 5 to 10 years?
There’s a lot we can expect in the next 5-10 years, and a lot will happen that almost no one will see coming. I think we’ll certainly see project schedules automatically generated from designs and a dramatic decrease in the cost of reality capture. I think we’ll see more robots on-site performing several repetitive activities. We may see meaningful advancements in mixed reality. And there is a fair possibility that we’ll see cranes and other heavy machinery operating themselves.