KUKA Robotics needs no introduction. A pioneer in industrial robotics and factory automation, KUKA combines mechatronics know-how with cloud technologies and mobile platforms to offer customized, intelligent automation solutions for a wide range of industrial robots with various payload capacities, suitable for almost any application.
Recently, I had an opportunity to interview Simon Whitton, Senior Vice President of Sales and Marketing of Kuka Robotics in North America, where he oversees KUKA’s welding, electronics, and mobility centers.
Simon has more than 30 years of experience in the robotics and electronics industries. He previously was at Swiss mechatronics company Stäubli. You can read the complete interview below:
Robots in factories and manufacturing facilities vastly improve efficiency and production by automating tasks like assembly, packaging, and palletizing products. Despite the benefits and progress in robotics in recent years, there persist several misconceptions about robotics. One of them, as we all know, is that robots are taking over the world. Thirty-seven percent of American workers between the ages of 18 and 24 are worried about robots and AI, eliminating their jobs. Self-driving trucks are already threatening the jobs of truck drivers, and it is causing massive panic in the profession. How do we handle this fear? Do you have any data to suggest that robots and AI are creating new, more fulfilling jobs for workers?
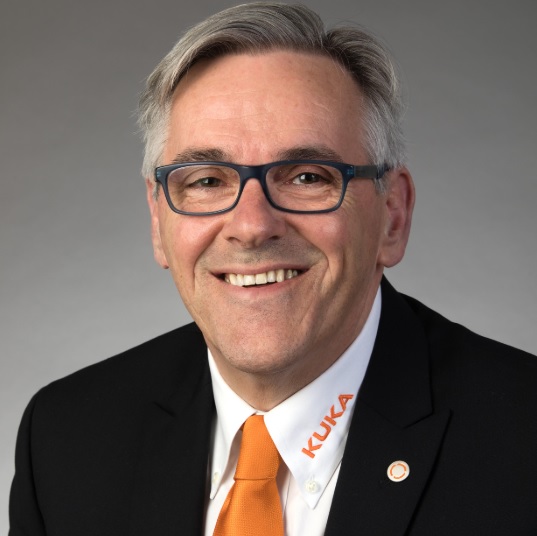
Education around automation is the key to handling fear of job elimination. It is vital to automation that workers are educated on the benefits of industrial workplace technology, like robots, to ease the fear of the changes ahead. For example, managers need to highlight that while automation will take over dull and monotonous tasks, this frees up workers’ time to take on higher-level work, like data analysis, robotic maintenance, and software development. The adoption of robotics is driven by the availability of labor rather than the cost of labor.
The second concern about robots is that they are unsafe. With sensors, speed-monitoring, and stopping abilities, today’s collaborative and mobile robots might be able to eliminate physical dangers. Can you explain how robots are helping us create a safer work environment?
Industrial robotics can diminish the likelihood of workplace injuries by addressing inattention and complacency. As workers become more comfortable with dangerous, repetitive tasks, they invest less time and attention to completing them, especially when they’re rushed or overworked. Robots help reduce human complacency-based errors by taking over monotonous tasks, like assembly line work, allowing workers to focus on higher-level and duties that keep them more engaged. The manufacturing workplace is also a highly regulated space, filled with mandates designed to improve worker safety. But signage, warnings, and barriers are often not enough to protect workers’ safety because these tactics rely on workers’ willingness to comply. Robotic safeguarding systems protect operators, engineers, programmers, and maintenance personnel by limiting their contact with hazardous machinery. Robotic safeguarding relies on limiting and presence-sensing devices and sensors to keep workers out of harm’s way when dangerous machinery is in use.
Many cobot manufacturers are making significant investments to improve the collaborative control of robots further and enhance user experience. For instance, they want to strengthen their human-machine interface (HMI) and the integration of AI to imitate the work of a human arm, with equivalent or better performance. Cobots need to have a deep understanding of human behavior to adapt the working patterns of multiple users to respond efficiently. Can you tell us about the new technologies transforming the robots’ ability to adjust their collaboration with human workers?
In the past, the collaboration between human workers and robots was hindered by the need for robots to remain behind cages. Now, sensors and vision systems have revolutionized the robotics industry. These technologies enable cobots to work alongside human workers without safety barriers. Proximity and motion sensors can determine when a worker is near, prompting robots to slow down or stop tasks that are too dangerous to complete in the vicinity of a human. Previously, robots were restricted to 2D vision, where only flat images could be seen. Many robots are now equipped with 3D vision systems, allowing them to accurately perceive their environment in the same manner as humans do. This technology permits robots to detect unforeseen changes to their environment and react accordingly. With robots and humans working collaboratively, the manufacturing industry will see more productivity and efficiency, which will allow us to advance even further in the space.
Tell us about Kuka Robotics. How is it transforming the world of industrial robotics and factory automation in 2020?
KUKA Robotics is one of the world’s leading suppliers of intelligent automation products and services. We have a long history dedicated to transforming the world of factory automation by providing customizable, automated systems, including industrial robots, software, controllers, and production systems. As Industry 4.0 and the IoT continue to grow in importance, KUKA is dedicated to merging its existing core of automation to connect robots to digitally networked processes to deliver maximum performance and efficiency.