In light of an international supply chain crisis and ongoing labor shortage followed by the COVID-19 pandemic, warehouses can barely hold on with peak season’s arrival. But while shipping vessels may be at a standstill, warehouses have a deus ex machina in place to keep them moving: robots.
To support warehouses through these difficult times, a leading robotics company inVia Robotics provides the next generation of warehouse automation solutions that blend the skills of people with autonomous mobile robots (AMRs) plus AI-driven software to support order fulfillment and returns and inventory management at varying scales.
To know more about how AMRs can enable warehouses to circumvent some of this season’s biggest challenges, such as workforce, productivity, and safer working conditions, we recently had an elaborate discussion with inVia’s co-founder and chief executive officer, Lior Elazary.
Lior has worked in the internet networking, robotics, software development, and enterprise architecture industries for over 20 years. He has led and directed a variety of teams that have worked on everything from back-office systems to enterprise-wide technologies.
Lior completed a master’s degree in computer science at the University of Southern California (USC), focusing on artificial intelligence (AI). He met his inVia co-founders while pursuing a Ph.D. in robotics at USC. Their collaboration sparked a passion for the transformative power of robots in increasing efficiency and productivity and, most importantly, in assisting people in living happier and more fulfilling lives.
You can read the complete interview below:
1. According to a report by DHL, 80% of warehouses are “still manually operated with no supporting automation.” Mechanized warehouses account for 15% of total warehouses, while only 5% of current warehouses are automated. Why does the warehouse automation penetration remain quite low in many cases? What is the COVID-19’s impact on the adoption of warehouse automation?
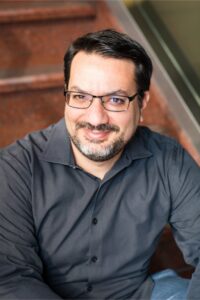
Automation hasn’t been widely adopted because it wasn’t affordable for most businesses – neither from a money nor a time perspective. Traditional automation systems cost millions of dollars and generally take 12-18 months to construct and implement. These traditional systems were fixed, literally bolted into the floors. So, they really were a construction project that was expensive, time-consuming, and by definition inflexible. On top of that, they took a very long time to deliver any return on investment, and in some cases, they never did. Only the 1%ers of the corporate world could afford them.
In the last several years’ technological advances have made computer processing power more readily available and affordable, and that has led to a new breed of automation that is accessible to any sized business. Two hallmarks of this newly accessible technology are its mobility and being able to pay for it as a service vs. purchasing the equipment as a capital expense. Robotics-as-a-service offerings are common now, and they offer businesses the ability to pay for the productivity of robots through a monthly subscription. They don’t have to purchase or maintain the equipment, and they immediately see a positive ROI.
COVID-19 exacerbated two problems that were already pressuring businesses to find more efficiencies in their fulfillment processes – unprecedented growth in e-commerce demand and a lack of labor to perform warehouse jobs. When stores closed, and warehouses could only have a minimal number of people in them safely distanced, these challenges became even bigger. Warehouses are at a point now where they have to automate to keep up with crushing demand and unavailable labor.
2. One common challenge in warehouse automation is that there are no off-the-shelf solutions – each system is customized to the individual customer’s business needs. Is it a good thing, or do we need more one-size-fits-all solutions? What is your approach?
While no two warehouses are exactly the same, they all have in common that they are orchestrating the movement of goods to achieve their daily SLAs or the agreements they have in place for on-time delivery. In that same spirit, we have a set of workflows and modules from which we choose the right combination to help our customers meet their SLAs. Part of our job is to help businesses reimagine workflows to find greater efficiencies than they had before. We take a look at the movement of goods, people, and other equipment in the warehouse to design a system that ensures they all continue to flow with minimal delays or idle time. That overriding system design is the same for every customer, and the way that it is integrated within their existing facilities and systems is where the customization comes in.
Since we sell our solutions as a service, we’re part of our customers’ daily operations. That means we’re helping them solve for the unexpected every day. So, our problem-solving skills have to be customized in order to be agile. E-commerce is a very dynamic space and isn’t off-the-shelf by nature. However, our standard systems are built to be flexible and innovative to accommodate the unanticipated.
3. The implementation of warehouse robotics is a sensitive subject. The primary fear surrounding automation is the loss of employment. How do you integrate people, processes, and systems to the right degree?
Our customers couldn’t find enough people to fill e-commerce warehouse jobs pre-pandemic, and it’s even worse now. Most of them see 100% turnover rates in just a matter of months for the jobs they’re able to fill, and many jobs just go unfilled. Within e-commerce, these aren’t jobs that have ever existed before. It used to be that we walked through the aisles to find the products we wanted to buy and then took them to the checkout counter to pay. Now, we sit at home to check out, but someone still has to physically go find these items we buy on a shelf and get them to our homes. So this is a net new need for labor at a time when labor is already scarce.
Our warehouses do still have people in them. There are many jobs in warehouses that are ideally suited for people, the ones that involve problem-solving and decision-making. There are other jobs that are ideally suited for machines, the ones that require repetitive, rote tasks. These kinds of tasks are actually unhealthy for people, causing repetitive stress and overuse injuries.
4. How do we evaluate the automation readiness of a warehouse? What are the signs that indicate whether a warehouse is ready to automate?
For many warehouses, the question is not “if” they’ll automate; it’s “when.” The idea that people should be performing a job like robots is inaccurate. For warehouses to be able to maintain fulfillment rates while providing a sound working environment, we need to switch the tasks that humans perform. These rote tasks should be left to the robots while people perform the more fulfilling parts of the job.
Any warehouse can be ready to automate with the new breed of robotics. Mobile robotics systems make it easy to overlay automation onto existing facilities without having to make major changes. The biggest part of an automation integration with mobile robots is the software side. Our robots, for example, can be deployed and productive in a couple of days.
5. Tell us about your Robotics-as-a-Service model. How does it knock down the biggest barrier to entry for automation–massive infrastructure investment–by offering automation as a subscription-based service?
inVia’s unique approach to robotics-as-a-service (RaaS) brings optimization to warehouses of any size. We employ a blend of autonomous mobile robots (AMRs) with AI-driven software to increase the productivity of a warehouse. We automate all fulfillment processes like picking, replenishment, cycle counting, and returns. The customer only pays for the productivity of the system. They don’t buy the equipment. We retain ownership, maintenance, and all the costs that go along with it.
6. Tell us about the new technologies and trends that will set a new path forward for warehouse automation in the next five years?
Warehouse automation is in its early stages, so many of the advances we’ll see over the next five years will be a refinement of algorithms and AI to make the automation incrementally better. We’ll see continuous improvements in order cycle times. For example, we’ve increased the throughput of our robots by 10% just in the past year, and we expect to increase it by even more next year. We’re continually improving the speed and precision of every movement the robots make.
Another major development we’ll see is more streamlined integration across all warehouse technologies. Over the next few years, we’ll see a steady increase in the adoption of automation technologies, and there will be increased momentum to link them all together. In another ten years, we’ll likely start to see “dark warehouses” where these facilities are 100% automated, and people are monitoring them remotely. They will include a number of different types of automation that have to be able to work together seamlessly.